How to Reduce the Drying Cost of Slime Dryer?
Coal slime contains a large amount of water, and its material viscosity is also relatively large. At present, coal slime materials have not been fully utilized. Therefore, in order to reduce resource waste and make full use of coal slime, it is necessary to dry the coal slime materials first. In the process of slime drying, as long as the quality of slime drying is maintained, how to reduce the production cost of slime dryer is a key problem.
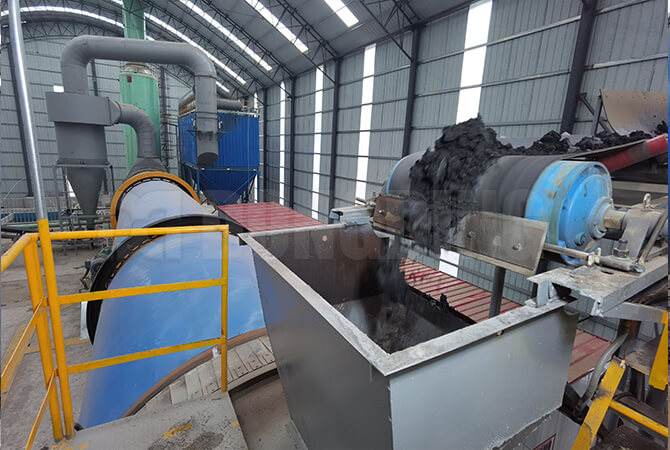
According to the current production technology and equipment, in order to reduce the cost of slime drying, the heat source and equipment structure should be considered first. At present, the common heat sources include coal, electricity, gas, oil, steam, biomass pellets, waste heat of boiler flue gas, etc. The use cost of these heat sources is different, and different heat sources have a great impact on the later cost input of equipment.
The slime drying equipment mainly conducts mass and heat exchange with the slime through hot air, so as to quickly evaporate the water in the slime. A special dispersing device is installed inside the rotary drum, which can disperse and stir the coal slime to speed up the mixing contact between the coal slime and hot air, not only improve the utilization of heat energy, but also improve the production efficiency of the drying equipment.
The initial moisture of coal slime is also an important factor affecting the drying cost. The higher water content in the coal slime, the more heat is required. Therefore, the hot blast stove needs to provide more heat energy for the slime dryer, which increases the fuel input cost. Generally, the initial moisture content of slime is about 30%-35%, which is relatively high for the rotary drum slime dryer. The coal slime can be used when it is dried to less than 15%.
The waste heat of some exhaust gas of the drying system can be reused to dry materials. Thus, it can reduce part of the waste circulation of the slime dryer, and also reduce the loss of heat source. Generally, the exhaust gas circulation volume is 20%-30%.
Besides, daily inspection, repair and maintenance of slime dryer are also very important. Therefore, the components can guarantee the stable operation and production of the drying equipment, reduce the frequency of equipment failure, and extend the service life of the equipment.
Operators shall strictly follow the manufacturer’s operating instructions to reduce equipment failures caused by human factors. In the case of uneven feeding, it is easy to cause a large amount of materials accumulation, which can affect the drying speed of slime. In order to reduce the production cost of slime dryer, it is necessary to maintain good operating habits to ensure the uniformity of feeding.
Users can select the coal slime drying equipment according to their actual production needs, so that the equipment can better handle materials and bring higher economic benefits to users.